Fully-Coupled 3D Fluid Dynamics Engine Simulation With The Nonlinear Harmonic Method
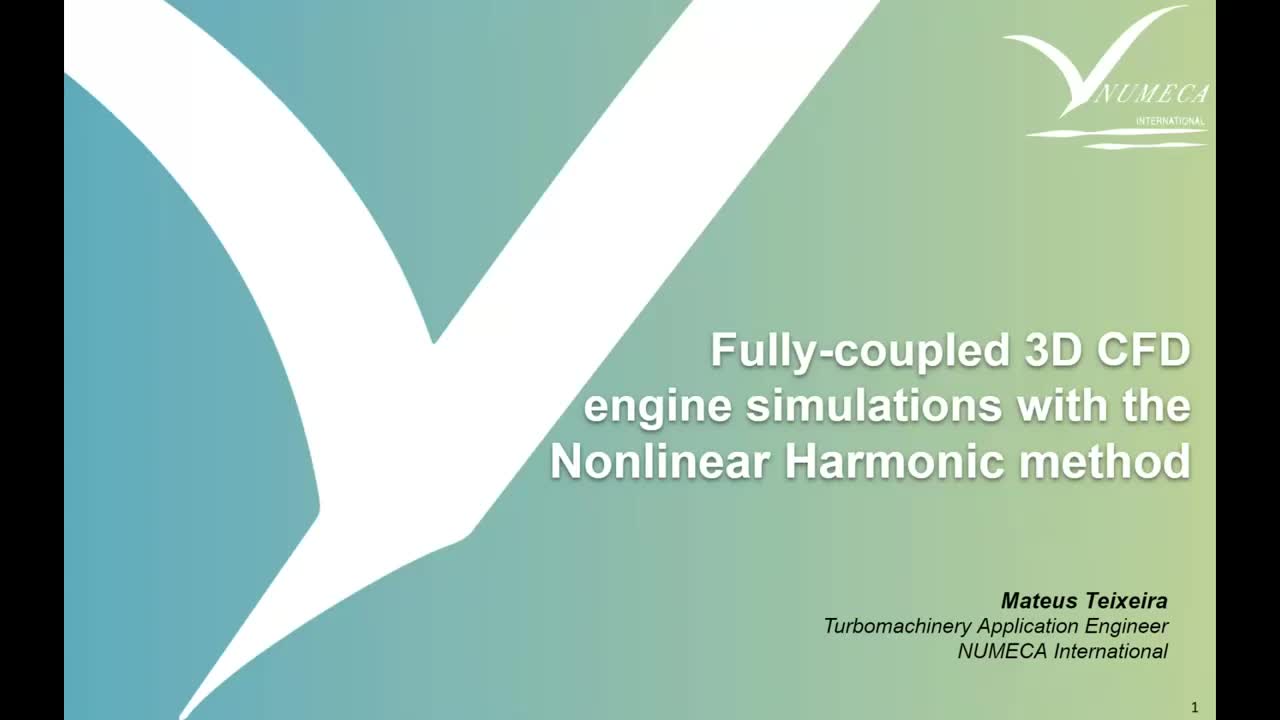
One of the many challenges when designing a micro gas turbine (MGT) engine is the overall complexity of the system and its consequent demand for accurate and holistic simulation tools. Such complexities can be exemplified by geometrical details (e.g. cooling holes, tight clearances) and by the interaction effects between components (e.g. compressor-turbine torque matching, temperature non-uniformities leading to excessive heating...).
Engine designers rely on a large variety of tools: from 1D/2D codes to high fidelity 3D computational fluid dynamics (CFD) for steady and unsteady flow physics modeling or even expensive experimental campaigns.
Nevertheless, cost and time dictate a component-by-component approach, with analysis of one or few components of the engine. Such methodology often requires assumptions for the boundary conditions and involves a considerable effort in coupling different component analysis tools, leading to a long and potentially error-prone process, frequently resulting in significant mismatches between numerical and real operating conditions.
NUMECA’s response to these requirements is the development of a full-engine 3D CFD simulation framework, from compressor inlet to exhaust hood, using one single tool. Simulations with the Nonlinear Harmonic Method (NLH) can provide high fidelity results with proper capturing of unsteady flows and inter-component interaction effects with a significant speed-up when compared to traditional full-unsteady methods.
In this 40-minutes webinar we will cover:
- An introduction to traditional full engine simulation and modeling approaches;
- NUMECA’s methodology for fully-coupled 3D CFD engine simulations;
- A case study of the unsteady aerodynamic analysis of the KJ66 MGT using the Nonlinear Harmonic Method presented in the 2019 ASME TurboExpo Conference;
- What’s to come on NUMECA tools for turbomachinery simulations.